Skip to content
By Larry Robbin, Executive Director of Robbin and Associates
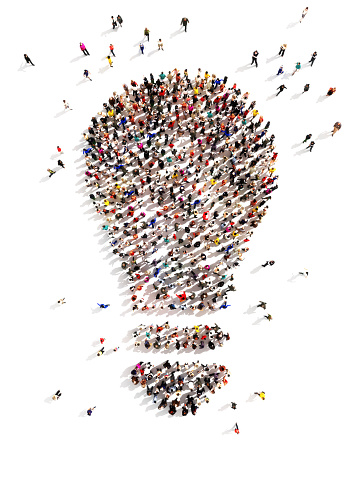
The answer is it takes 2,500 people
in the workforce development field to screw in a light bulb!
Now you are probably asking yourself how can it take 2,500 people in the workforce development field to screw in a light bulb? Here is the answer. First of all, it takes 100 board members to determine whether or not screwing in light bulbs fits with the mission statement, vision statement and strategic plan of the organization. Since there are no light bulbs screwed in while they are debating this initiative, they will be sitting in the dark. They are often in the dark any way metaphorically speaking so this will come as nothing new to them. Then it takes 100 labor market information specialists to determine whether or not being a light bulb screwer is a high demand and high wage occupation. Then it takes 100 planners, managers, analysts, accountants and program developers to develop the plans, policies, procedures, budgets and let us not forget memorandums of understanding for screwing in light bulbs. Then it takes another hundred people to design the one year training program that will teach people how to screw in light bulbs.
Then once the program gets started, it takes 100 outreach workers to recruit the light bulbs for screwing in. It could take a lot of time if the light bulbs are really resistant to being screwed in. You might call these light bulbs the hard-to-screw. Then it takes 100 eligibility workers to determine if each specific light bulb meets the 453 program requirements for being screwed in. The light bulbs will have to bring in extensive documentation about how they were manufactured, packaged and shipped and whether or not they have been screwed in before. Then it takes 100 people to decide whether or not some light bulbs are self sufficient enough to screw themselves in and to determine which ones need assistance. If a light bulb cannot screw itself in then it takes 200 case managers to counsel the light bulbs so they can get motivated and overcome their barriers to being screwed in.
Of course, a screwing in plan has to be developed with all 783 forms filled out correctly. Then it takes 100 people to recruit and assess the screwers who will screw in the light bulbs. Then it takes 100 light bulb screwing certified teachers to teach the light bulb screwing in class to the screwers. Then once the light bulbs graduate it takes 100 job developers to find the sockets that want a light bulb screwed into them by a certified screwer. If the sockets are reluctant to be screwed into the job developers can offer them screwing in tax credits as an incentive. Then once the light bulbs are screwed in it, takes 100 retention specialists to make sure they stay screwed in and to see if there is anything else that can be done for the socket to make them happier after their screwing into experience.
Then it takes 100 data entry people to enter the data about the light bulbs being screwed in. This would include: Of the light bulbs that were eligible to be screwed in, how many actually got screwed in? What were the light bulbs barriers to being screwed in? How long did it take to screw in the light bulbs? How long did the light bulbs stay screwed in? What was the average cost of a light bulb being screwed in? The answer to this was that with so many people and so much time involved in the light bulb screwing initiative that the average cost of screwing in a light bulb was about $1,300,000 per bulb. How many light bulbs fell out after being screwed in? What did the light bulbs learn from being screwed in that was different from what they knew before they were screwed in? What was the customer satisfaction level of the sockets about being screwed into and would the sockets like to be screwed into again? How many light bulbs advanced in wattage or went on to larger and better sockets? And finally – Did the screwers make a career out of screwing in light bulbs or did they get non-screwing in related jobs? Then you need 100 evaluators to determine if the light bulb screwing in initiative really worked, met all its performance standards and had a good return on investment. These people would make these determinations by looking at the data, interviewing the light bulbs, sockets and the screwers.
Now if you have been keeping track of the numbers, you know that this only accounts for 1500 of the 2500 workforce development professionals that it takes to screw in a light bulb. So where are the other 1000 workforce development professionals that it takes to screw in a light bulb? Don’t worry – the other 1000 are the light bulb screwing in initiative monitors. The screwing initiative monitor’s job is to flip the light switches to make sure the light bulbs go on!!! So now you understand why it takes 2,500 workforce development professionals to screw in a light bulb!
The owner of this website has made a commitment to accessibility and inclusion, please report any problems that you encounter using the contact form on this website. This site uses the WP ADA Compliance Check plugin to enhance accessibility.